- Amministrazione Kustom Service
- Epoxy Resin
- 0 likes
- 9784 views
- 0 comments
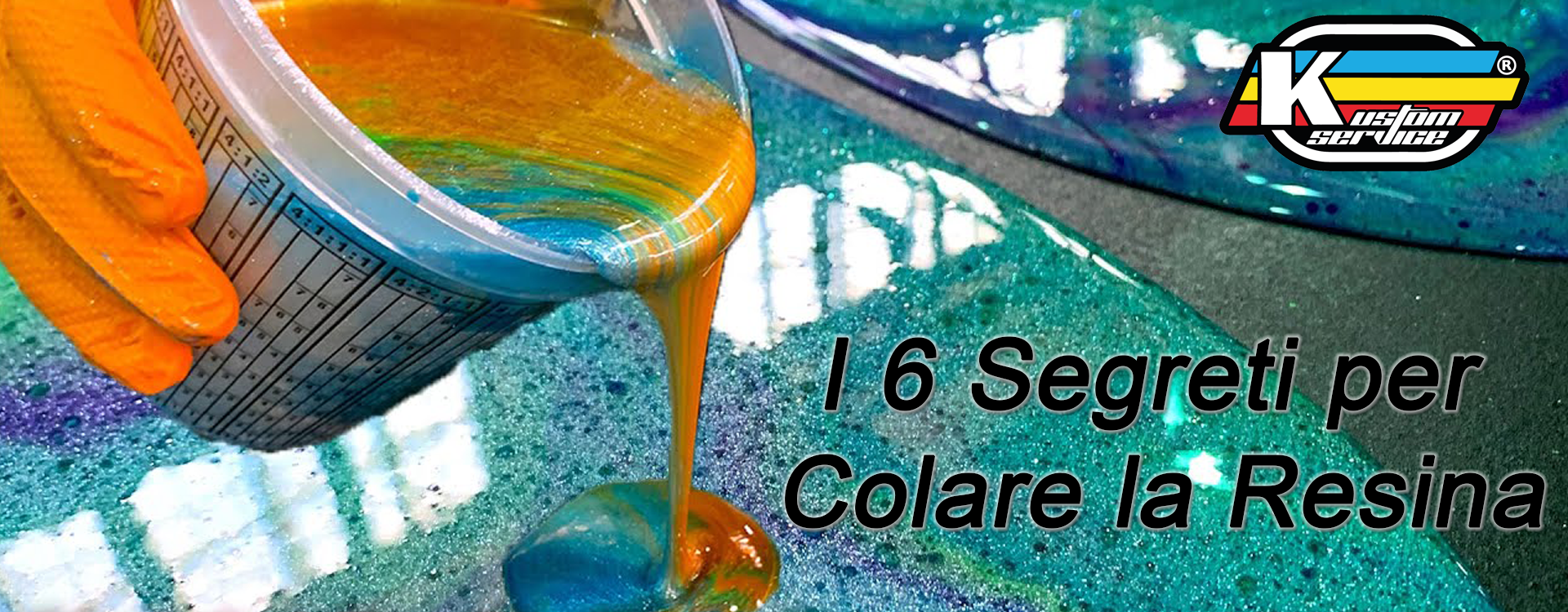
Pouring resin is an art—do it right!
The first step to a perfect pour is ensuring the ambient temperature is between 18 and 22 degrees Celsius.
Since it’s not always possible to achieve this, we ask you to follow these simple rules to improve your work.
Following them will help you save money and achieve beautiful results from the start.
RULE 1
Always mix the base and the hardener for at least 2–3 minutes. It may seem long, but it’s not. The components of epoxy resin are very dense, so it’s crucial to ensure they are fully combined.
If you are mixing 1 kg of resin or even 500 g, we always recommend using a mixer attachment with a drill. Believe it or not, mixing by hand is problematic. The cutting and mixing force of a drill with a mixer attachment cannot be matched by human hands.
RULE 2
Maintaining the correct temperature is ideal, but we know this is only possible when working indoors or during the summer. So how can you minimize risks?
It’s simple: after mixing the components, wait 30 minutes in winter or 20 minutes in summer before pouring.
This ensures that the two components have begun to react and generate heat—heat that provides two key benefits:
- The resin becomes more fluid, making it easier to pour.
- Air bubbles trapped in the resin rise to the surface, where they can be removed with a heat gun, resulting in a cleaner pour.
RULE 3
If you’re working in winter or in a very cold environment, warm both components (A and B) before mixing them.
You can use a heat gun to warm the containers for a few minutes or place them in a warm water bath.
This will make the components more fluid and easier to mix. If the resin appears slightly cloudy, heat will return it to its transparent state. In winter, Component A can sometimes become opaque due to the cold. If you notice this, don’t worry—it’s normal and can be fixed with heat.
RULE 4
Always pour a layer thickness as recommended in the product’s technical datasheet.
- If your resin is designed for 2 cm thickness, pour 1.5–2 cm maximum, no more.
- If it’s designed for 5 cm, pour 5 cm maximum, no more.
Understand that if the maximum recommended thickness is 2 cm, it’s safer to stay slightly below that.
Stay close to your pour and, every 15 minutes, remove excess bubbles with a heat gun.
This ensures a compact, glass-like, transparent layer free of bubbles.
RULE 5
To pour resin successfully, understand that the larger the volume of resin poured, the more heat it generates.
- The more heat generated, the greater the risk of the resin turning yellow.
- Excessive heat also increases the risk of the resin warping, bending, or even cracking, damaging any objects embedded within it.
If your resin is rated for a maximum thickness of 2 cm, this doesn’t mean you can’t pour 2.5 cm, but it depends on the total quantity being poured.
For example:
- Pouring 30 kg over a 3-meter-long table at a thickness of 2 cm might work fine.
- However, pouring 30 kg into a 1-meter-long space at 4 cm thickness is very risky.
For this reason, it’s always better to stay within the manufacturer’s recommended limits.
RULE 6
This may be the most important rule of all: seal the wood and close its pores.
Wood is alive and breathes, so in addition to ensuring it’s completely dry, you must also seal its pores. If not, there’s a real risk that the resin, as it cures, will trap air from the pores and release it.
If your pour looks perfect when completed but, after 12 hours, you notice hundreds of microbubbles near the wood, it means you didn’t seal the pores properly, and they caused the problem.
For this reason, we’ve developed specific products to quickly seal wood without wasting time.
You can find these products in our dedicated wood resin section:
LINK
THE RIGHT PRODUCTS
Kustom Service produces two resins and several pore sealers:
- K Crystal: For layers up to 2 cm. LINK
- X Crystal with slow hardener: For layers up to 5 cm. LINK
- K5: A product that acts as both a base coat and an extra-glossy finish. LINK
Comments (0)